Low Pressure Troubleshooting Solutions information from Cat Pumps ®
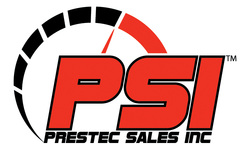
Worn Nozzle
Worn nozzle(s) are the most frequent cause of low pressure. Never adjust the pressure regulating valve to compensate for worn nozzles. This will result in overpressure and possible damage to the pump. Replace nozzle(s) with the proper size when pressure drops or on a regular maintenance schedule. Remember to factor in your 5-10% by-pass flow in your nozzle size calculation.
Air Leak
In Inlet Plumbing can Keep connecting fittings like elbows and tees to a minimum. Use PTFE liquid or tape on all connections. Inspect all connections at regular service intervals.
Pressure Gauge Malfunction
The pressure gauge is the pulse of your system. It will tell you if something is not functioning correctly in your system. No reading indicates the gauge is probably damaged and needs to be replaced. Check pressure with new gauge and replace as needed.
If the pressure is fluctuating, possible system issues could be:
Regulator/Relief Valve Malfunction
Check to see if the regulator and relief valve performance range covers your system performance. If the system spec is out of the valve range, it will not function properly.
The regulating/relief valve may become clogged from debris in the pumped liquid. Check liquid supply for contamination. Inspect the supply tank. The feed line from your supply tank to your pump should not come from the bottom where it can pick up residue.
A worn internal part in the valve such as a piston stem may have become lodged. Clean and service the valve with repair kit on the same schedule as your pump seals. Reset primary valve and secondary relief valve to system pressure.
Worn Seat or Valves
Seats and valves are wear items and should be replaced periodically. See the attached chart for more information. Replacement valve kits are available and include the retainer, spring, valve, seat and necessary o-rings to complete the maintenance.
Conditions that can accelerate the wear to valves and seats include:
Inlet Filter Clogged or Improperly Sized
A clogged inlet filter can be a serious issue for your system. Initially pressure may drop, but ultimately serious damage will result due to lack of liquid to the pump.
Worn Seals
Seals are wear items and require periodic replacement. Please refer to the attached chart for proper maintenance schedule information. Seal kits are available and part number can be found on your pump datasheet. Standard Seal Kits include the Lo-Pressure Seals, Hi-Pressure Seals and necessary o-rings for standard maintenance.
Typical conditions that accelerate wear to the seals include:
Starving the Pump of Liquid
Starving the pump or insufficient liquid to the pump inlet is one of many causes of low pressure. To avoid starving the pump:
Stressful Inlet Conditions
Check the line size to the pump inlet. It is preferable to use reinforced flexible hose at the pump inlet and eliminate excessive elbows.
An under sized line or collapsing line will starve the pump of liquid. It will give a low pressure or fluctuating pressure reading on the gauge and result in damage to the pump.
Other causes of inlet stress are:
NOTE: the C.A.T. will not function with negative inlet pressure or correct for starvation.
Leaky Discharge Hose
Replace the high pressure hose when it becomes extemely worn or cracked.
Check for damage to the fitting attaching the hose to the system and secure connections with PTFE liquid or tape.
Always use a hose that is rated for the system performance.
Belt Slippage
Belts are wear items and should be periodically replaced. Check for proper tension. Ensure you are using the correct belt type, length and number of belts to assure adequate horsepower.
Worn nozzle(s) are the most frequent cause of low pressure. Never adjust the pressure regulating valve to compensate for worn nozzles. This will result in overpressure and possible damage to the pump. Replace nozzle(s) with the proper size when pressure drops or on a regular maintenance schedule. Remember to factor in your 5-10% by-pass flow in your nozzle size calculation.
Air Leak
In Inlet Plumbing can Keep connecting fittings like elbows and tees to a minimum. Use PTFE liquid or tape on all connections. Inspect all connections at regular service intervals.
Pressure Gauge Malfunction
The pressure gauge is the pulse of your system. It will tell you if something is not functioning correctly in your system. No reading indicates the gauge is probably damaged and needs to be replaced. Check pressure with new gauge and replace as needed.
If the pressure is fluctuating, possible system issues could be:
- Poor inlet condition
- Malfunctioning regulating device
- Worn seals and/or valves
Regulator/Relief Valve Malfunction
Check to see if the regulator and relief valve performance range covers your system performance. If the system spec is out of the valve range, it will not function properly.
The regulating/relief valve may become clogged from debris in the pumped liquid. Check liquid supply for contamination. Inspect the supply tank. The feed line from your supply tank to your pump should not come from the bottom where it can pick up residue.
A worn internal part in the valve such as a piston stem may have become lodged. Clean and service the valve with repair kit on the same schedule as your pump seals. Reset primary valve and secondary relief valve to system pressure.
Worn Seat or Valves
Seats and valves are wear items and should be replaced periodically. See the attached chart for more information. Replacement valve kits are available and include the retainer, spring, valve, seat and necessary o-rings to complete the maintenance.
Conditions that can accelerate the wear to valves and seats include:
- Abrasives in the liquid
- Excessive heat
- Cavitation
- Starvation
- Harsh chemicals
- Hard water
Inlet Filter Clogged or Improperly Sized
A clogged inlet filter can be a serious issue for your system. Initially pressure may drop, but ultimately serious damage will result due to lack of liquid to the pump.
- Check supply tank for contamination
- An open supply tank can pick up debris, so we reccomend only installing a cover
- Check and clean filters on the same schedule as replacing your seals
- Your filter cleaning schedule may need to be more frequent, if the liquid being pumped is recycled or dirty
- If pumping extremely dirty liquid, dual filters or larger filters may be necessary
- When using a holding tank, do not feed the pump from the bottom of the tank
Worn Seals
Seals are wear items and require periodic replacement. Please refer to the attached chart for proper maintenance schedule information. Seal kits are available and part number can be found on your pump datasheet. Standard Seal Kits include the Lo-Pressure Seals, Hi-Pressure Seals and necessary o-rings for standard maintenance.
Typical conditions that accelerate wear to the seals include:
- Abrasives in the liquid
- Excessive heat
- Cavitation
- Starvation
- Harsh chemicals
- Hard water
Starving the Pump of Liquid
Starving the pump or insufficient liquid to the pump inlet is one of many causes of low pressure. To avoid starving the pump:
- Ensure all valves are open in the supply line before starting your pump
- Check the total demands from the main supply line to assure there is adequate liquid supply when all systems are operating
- Check for line restrictions and minimize elbows and fittings
- Make certain the inlet line is at least the size of the pump inlet port, preferably one size larger
- Avoid Rigid Plumbing
- Flexible hose should be installed the last 3-6 feet before the pump inlet.
- When using longer inlet feed lines, a booster pump and a C.A.T. should be considered
- Properly seal all connections with PTFE tape or liquid for air tight connections
- Confirm your liquid temperature is within the maximum limits of the pump
- If temperature are above 130F, a pressurized inlet supply is required
- If returning the by-pass to the pump inlet, install a Thermo Valve in the by-pass line to bleed off excessively hot liquids
- Connect the supply line from supply tank to the pump at least 3-4" above bottom to avoid picking up any sediment
- The pump supply line from the tank should be plumbed from the opposite side of the tank than the by-pass return and tank fill line.
- This will minimize air bubbles caused by agitation being drawing into the pump.
- The supply tank should contain at least two baffles to help expel air bubbles.
- If returning a high volume of warm liquid to the holding tank, oversize the tank to allow for adequate cooling before going back to the pump.
Stressful Inlet Conditions
Check the line size to the pump inlet. It is preferable to use reinforced flexible hose at the pump inlet and eliminate excessive elbows.
An under sized line or collapsing line will starve the pump of liquid. It will give a low pressure or fluctuating pressure reading on the gauge and result in damage to the pump.
Other causes of inlet stress are:
- High inlet pressure from booster pumps
- Spiking return valves
- Rigid plumbing
- Long feed lines
NOTE: the C.A.T. will not function with negative inlet pressure or correct for starvation.
Leaky Discharge Hose
Replace the high pressure hose when it becomes extemely worn or cracked.
Check for damage to the fitting attaching the hose to the system and secure connections with PTFE liquid or tape.
Always use a hose that is rated for the system performance.
Belt Slippage
Belts are wear items and should be periodically replaced. Check for proper tension. Ensure you are using the correct belt type, length and number of belts to assure adequate horsepower.