Pulsation Solution(s) from Cat Pumps ®
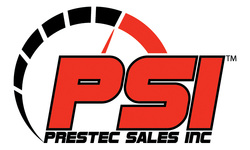
Stressful Inlet Conditions
Pulsations can occur when there is a restriction in the inlet line or air is being drawin with the liquid. Proper line size and adequate liquid to the pump are critical. Clean inlet filters regularly. Increase the size of your filter or use dual filters if clogging occurs too frequently. Check all connections and use PTFE liquid or tape for airtight connections. Make certain the line size is at least the size of the pump inlet [preferably one size larger] and elbows are kept to a minimum. Flexible hose is recommended 3-6" before the pump inlet. A properly baffled supply tank will eliminate air from the inlet line. Some liquids require a pressurized inlet and a C.A.T. to stabilize inlet pressure.
Stuck Inlet or Discharge Valves
This condition is typically a result of liquids that easily set-up, are high viscosity or contain suspended solids. Check supply tank for contamination. Review the viscosity of the liquid. CAT PUMPS operate best with liquids up to 500CPS or 2500SSU. Some liquids change in nature by heat, velocity as it moves through the pump, exposure to atmosphere or blending with other liquids. Some liquids require a flush prior to any dormant cycles to prevent set-up or pump contamination. Review maintenance schedule.
Worn or pitted inlet/discharge valvesWorn or pitted valves are typically a result of poor inlet conditions, cavitation or starvation. Harsh liquids or excessive heat may also be a cause. Check supply tank for proper size and excessive air bubbles. Supply tank should contain at least two baffles. The fill line into the tank should be on the opposite side as the discharge line out to the pump. Review the pumped liquid for abrasives and install proper filtration. Check the pH of the liquid to be certain it falls within the 5 to 9 range. Check for excessive temperature and install Thermo Valve in by-pass line or increase supply tank size to allow for cooling. On systems above 130 F, pressurize the inlet and install a C.A.T.
Stressful discharge plumbing
Long discharge lines can create a water hammering effect when the pump is not properly isolated. Flexible hose at the pump inlet and prior to any hard plumbing in the discharge line is recommended. Install a pulsation dampener on the discharge manifold.
Pulsations can occur when there is a restriction in the inlet line or air is being drawin with the liquid. Proper line size and adequate liquid to the pump are critical. Clean inlet filters regularly. Increase the size of your filter or use dual filters if clogging occurs too frequently. Check all connections and use PTFE liquid or tape for airtight connections. Make certain the line size is at least the size of the pump inlet [preferably one size larger] and elbows are kept to a minimum. Flexible hose is recommended 3-6" before the pump inlet. A properly baffled supply tank will eliminate air from the inlet line. Some liquids require a pressurized inlet and a C.A.T. to stabilize inlet pressure.
Stuck Inlet or Discharge Valves
This condition is typically a result of liquids that easily set-up, are high viscosity or contain suspended solids. Check supply tank for contamination. Review the viscosity of the liquid. CAT PUMPS operate best with liquids up to 500CPS or 2500SSU. Some liquids change in nature by heat, velocity as it moves through the pump, exposure to atmosphere or blending with other liquids. Some liquids require a flush prior to any dormant cycles to prevent set-up or pump contamination. Review maintenance schedule.
Worn or pitted inlet/discharge valvesWorn or pitted valves are typically a result of poor inlet conditions, cavitation or starvation. Harsh liquids or excessive heat may also be a cause. Check supply tank for proper size and excessive air bubbles. Supply tank should contain at least two baffles. The fill line into the tank should be on the opposite side as the discharge line out to the pump. Review the pumped liquid for abrasives and install proper filtration. Check the pH of the liquid to be certain it falls within the 5 to 9 range. Check for excessive temperature and install Thermo Valve in by-pass line or increase supply tank size to allow for cooling. On systems above 130 F, pressurize the inlet and install a C.A.T.
Stressful discharge plumbing
Long discharge lines can create a water hammering effect when the pump is not properly isolated. Flexible hose at the pump inlet and prior to any hard plumbing in the discharge line is recommended. Install a pulsation dampener on the discharge manifold.